Flexo Platemaking Automation and Standardization: a Reality Thanks to Esko, Vianord and Inci-Flex
On the occasion of its 20th anniversary, Inci-Flex presented a revolutionary, completely automated flexo platemaking process, assuring quality, standardization and productivity.

The Challenge:
Reduce amount of manual steps.
The Solution:
Install Esko CDI Crystal 5080 XPS.
The Benefits:
Create plates faster, without human intervention.
Case Study Summary
Inci-Flex’s platemaking department has four CDI’s with a 5080 imaging size, a Kongsberg XN 22 cutting table with the Digital Flexo Suite, and the entire state-of-the-art prepress software suite from Esko (including PackEdge, ArtPro, Plato, DeskPack, Studio, Automation Engine, Imaging Engine and Color Engine). When Inci-Flex installed the first CDI Crystal 5080 XPS from Esko, it truly differentiated itself in the marketplace. Instead of sending a flexo plate through up to nine manual steps, this groundbreaking solution creates plates faster, without any human intervention. The automation of digital imaging and LED UV exposure improves consistency, processing speed and overall ease of use. It not only frees up valuable operator time, but also reduces maintenance and the footprint required for flexo equipment.
A process that took nine steps has been reduced to one single step, all without operator intervention.
Automating the plate production process and introducing standardization is the only way to increase efficiency and reduce costs.
The long-term relationship between Esko and Inci-Flex, a flexo and gravure prepress business based in Fisciano (Salerno province), Italy, has been based on reciprocal trust and the reliability assured by Esko solutions. This Italian company has always been a technology pioneer in testing new production approaches, an attitude that found a perfect match in Esko’s commitment to innovative technology. Inci-Flex specializes in the production of plates for printing of flexible packaging and labels for the food and beverage industries, as well as other sectors. The company is dedicated to providing its customers with the highest quality plates, which can only be achieved by staying up-to-date with the latest innovative technology.
Inci-Flex’s platemaking department has four CDI’s with a 5080 imaging size, a Kongsberg XN 22 cutting table with the Digital Flexo Suite, and the entire state-of-the-art prepress software suite from Esko (including PackEdge, ArtPro, Plato, DeskPack, Studio, Automation Engine, Imaging Engine and Color Engine). When Inci-Flex installed the first CDI Crystal 5080 XPS from Esko, it truly differentiated itself in the marketplace. Instead of sending a flexo plate through up to nine manual steps, this groundbreaking solution creates plates faster, without any human intervention. The automation of digital imaging and LED UV exposure improves consistency, processing speed and overall ease of use. It not only frees up valuable operator time, but also reduces maintenance and the footprint required for flexo equipment.
Celebrating history while looking ahead
To commemorate its 20-year anniversary, Inci-Flex hosted a gathering for employees, customers and friends. This important event not only looked back on 20 years of successful leadership by managing director Vincenzo Consalvo and an additional 15 years by his father Carmine, it also told an innovation story full of challenges faced and overcome.
Inci-Flex’s spirit of innovation was at the heart of a new project unveiled at the event. Vincenzo Consalvo explains, “The installation of the processing unit by Vianord and the automation assured by the CDI Crystal 5080 XPS from Esko got us thinking about how to even further automate and standardize the platemaking process. We collaborated with our long-time partner Esko and our new supplier Vianord to develop a linear process. Linked by a purpose-built Smart Bridge, the plate begins its journey in the Crystal system and ends in the Vianord Evo 5 processing unit. Once a plate is placed on the CDI, it is not touched again until the whole production process is complete. With this system, a process that took nine steps has been reduced to one single step, all without operator intervention.”
“The three partners – Esko, Inci-Flex and Vianord – leveraged their competencies and know-how and worked hard for several years to create this end-to-end solution. It was not an easy task, but it delivered exactly what we needed: complete automation of the platemaking process. Not only will it decrease turnaround time, it will help us grow and adapt with the rapidly evolving flexo platemaking industry so we can respond to our customers’ most challenging issues and produce the finest plates in the industry.”
During the event, visitors had the opportunity to see all departments within Inci-Flex, including this revolutionary automated platemaking solution. Consalvo concludes, “Automating the plate production process and introducing standardization is the only way to increase efficiency and reduce costs, a critical requirement in today’s highly competitive environment. If our event is any indicator, this fully automated plate production process will generate a huge amount of interest in the industry. We are thrilled to have been part of this important development!”
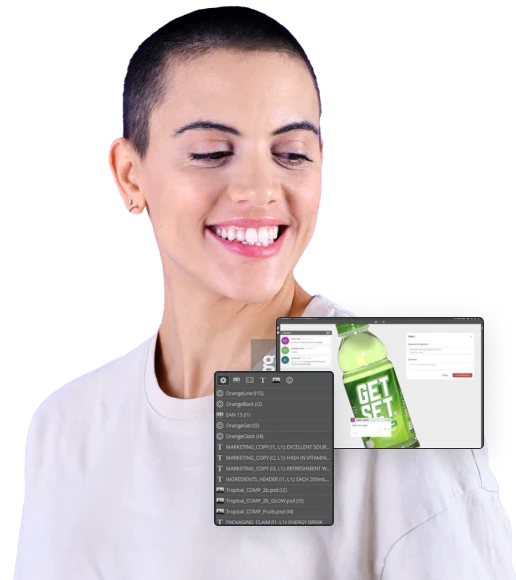