Packaging suppliers are well aware of the “unattainable triangle” of time, cost, and quality.
This means they find it nearly impossible to achieve all three simultaneously. Any combination of the two is attainable, but not all three.
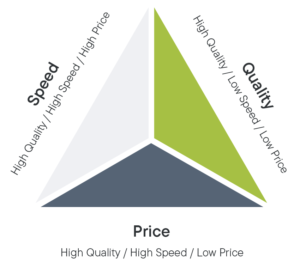
However, workflow automation offers a potential pathway to balancing these priorities.
In this article, we’ll discuss how a completely automated and connected workflow can boost accuracy, quality, and service in an increasingly competitive industry, securing a competitive edge in flexo platemaking.
Flexographic Plate Production
The platemaking set up of today’s typical prepress department or tradeshop incorporates numerous manual steps and several touchpoints. A basic process includes:
-
The preparation of the plate layout and separations to be sent to the imager
-
The retrieval of plate material from storage and transfer of the material to the exposure unit to be manually loaded
-
The entry of data into the exposure unit where the back of the plate is then exposed.
-
The manual unloading of the plate and the transferring of it to the imaging unit
-
The loading of the plate, entering of data, and imaging of plate
-
The unloading of the plate and manual transfer back to the exposure unit to be loaded for main exposure
-
The completion of final data entry in the exposure unit and the completion of the main plate exposure
-
The unloading of the plate and transfer to the processing unit for washing, drying and UV finishing
-
The final cutting and packing before transferring to the shipping department or press hall
With so many manual data entry points, the likelihood of human error is high. Additionally, physical movement of materials takes an operator’s time and attention.
Clearly, automating this process will both simplify and streamline it, resulting in significant process efficiency and cost reductions.
Achieving Complete Automation of the Platemaking Process
Complete digitization, automation, and connection of the prepress and platemaking process reduces the number of devices involved. Let’s explore how Esko solutions can simplify the platemaking process.
1. Esko Flexo Engine
The Flexo Platemaking Module is designed to enable a fully automated platemaking workflow from the RIPped files all the way to the exposed plate on a CDI Crystal XPS, without operator intervention. This completely digitized, automated and connected process now enables lights out file preparation for those converters who are typically using one or two plate types. For the busy tradeshop that needs to make a lot of last-minute decisions, semi-automated merging is also available.
Flexo Engine provides a dashboard overview of the status of a job in the device queue. Jobs can quickly and easily be placed in queues, and queues can be modified as needed. This saves valuable operator time, minimizing the need for interactive and time-consuming tasks. It virtually eliminates errors in the platemaking process and speeds time to the shipping department or press.
Flexo Engine also enables operators to receive detailed reporting about the exposed plates, including waste factors and time lapses, as well as offering insight to plate usage, type of plate and waste rates, as well as how much time it took to expose the merged plate, resolution and imaging technology. The connectivity enabled with Flexo Engine provides operators with a range of useful feedback for further optimization.
Don’t just take it from us! Our customers share their sentiments, stating, “We were looking to make an investment in a software solution that would enable the team to do more work with the same headcount, while also making the process error-free, controlled and sustainable.” − Anıl Ağcabay, Automation Specialist, Biriz Flexible
2. Esko CDI Crystal XPS Technology
In terms of achieving the ultimate goal of solving the plate quality, speed and cost challenge, the combination of the CDI Crystal flexo imager with the XPS Crystal exposing unit offers a perfect, consolidated flexo platemaking workflow with the highest return on investment.
Redefined from scratch, the integration and automation of the digital imaging and LED UV exposure processes improves consistency and overall ease of use for prepress operators.
This solution not only frees up valuable time, but also reduces maintenance and the footprint of the flexo equipment, keeping costs to a minimum.
The CDI Crystal XPS excels in efficiency and offers distinct benefits, such as:
• Reduction of manual steps by 50%
• Reduction of errors by 50% – less plate waste
• Reduction of operator time by 73%
Click here to find out more about the benefits of integrated CDI Crystal XPS technology.
3. Esko PlateHandler
Finally, in the plate room, a prepress operator is usually required to manage multiple devices to produce a plate, which may result in an increased risk of errors.
The Esko PlateHandler connects the CDI Crystal imaging unit with the XPS Crystal exposure technology. This reduces the number of operator touchpoints and minimizes the costs of operation. It does so by eliminating the need for an individual to move between machines transferring the material at various stages of the plate production process. Integrating platemaking equipment with Esko PlateHandler frees up to 50% of the prepress operator’s overall time, enabling attention for more value-adding tasks such as quality control, plate storage and plate mounting.
“We’ve gone from moving plates from machine to machine, to a streamlined, integrated and automated process that simply takes the push of a button to operate.” − André Vandepitte, Prepress Manager, Reynders, Belgium
4. Esko Platefeeder-S
The Esko Platefeeder-S has been designed to solve a number of common issues in the typical platemaking facility.
First, when plates are transferred manually from storage to the CDI, they can easily become damaged and distorted. The Platefeeder-S enables distortion-free transportation of plates. Importantly, the table can be tilted to pass through doors and docked onto the CDI to take care of perfect plate positioning and the digital connection to the CDI Crystal.
Second, integrating the PlateFeeder-S into the setup enables the positioning of an additional plate for automated transportation into the CDI Crystal immediately when available, boosting productivity.
Additionally, the operator now only needs to attend the machine once within each imaging cycle to load a new plate and unload the exposed plate from the XPS Crystal. This results in more flexibility in managing other tasks, for example, quality control, operating processing equipment or plate cutting.
Finally, plates must always be positioned accurately to prevent plate damage. With manual positioning, this is prone to errors and can be time intensive. With the PlateFeeder-S, once docked, it becomes visible on the CDI touchscreen and integrates into the automated workflow enabling the operator to position a new plate at any time during the imaging process.
Built-in sensors on the PlateFeeder-S also secure accurate plate loading via the PlateHandler, avoiding plate waste and further errors. With the plate material pre-loaded, the PlateFeeder-S eliminates 100% of the plate loading idle time on the CDI Crystal XPS. This results in uninterrupted platemaking, reducing system idling by up to 40% and delivering a 40% reduction in human touchpoints.
With a CDI Crystal XPS with PlateHandler and PlateFeeder-S working continuously with optimum throughput and minimum operator attention, the overall impact can be an increase in plate making productivity of up to 15%.
The Benefits of Complete Platemaking Automation
With a completely integrated and automated prepress and platemaking process, prepress operators are able to secure a wide range of benefits that challenge the myth of the unattainable triangle.
By integrating Esko Flexo Engine software and CDI Crystal XPS hardware technology with automatic plate feeding and handling, businesses can work towards the capability for lights out production with a significant boost to quality, efficiency and cost management.
This uninterrupted platemaking process also means machines do not have to stop for job data input, material feeding, or plate handling, resulting in less downtime and idling of equipment boosting overall equipment effectiveness (OEE).
Finally, with a reduction in operator attention and manual intervention, fewer human errors and less waste occurs, boosting accuracy and quality and ensuring customer satisfaction.
Not sure which flexo imager is right for you? Take our quiz to find out!
Book a discovery call to learn more.