Albéa maximiza la eficiencia y mejora la colaboración con los clientes con WebCenter de Esko
La empresa líder en fabricación de packaging para cosmética aprovecha la digitalización para lograr aumentar la eficiencia y satisfacer a sus clientes.
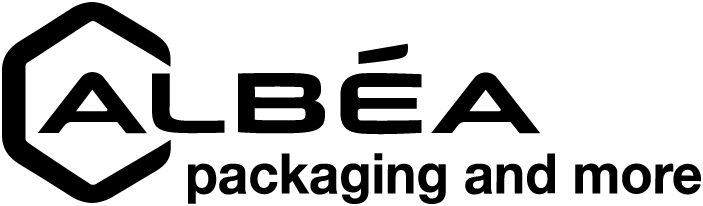
El cliente
Albéa, Gennevilliers, Francia
Albéa es el mayorista de packaging para cosmética número uno a nivel mundial; fabrica packaging y soluciones para la belleza, desde tubos y pintalabios hasta rímel, aplicadores y demás. En calidad de proveedor de packaging para el sector de la belleza, Albéa sirve tanto a marcas líderes ya establecidas como a empresas emergentes del mercado nacional e internacional.
La compañía cuenta con 31 centros de fabricación en 13 países y colabora con proveedores en otros estados. Albéa se ha ganado una buena reputación y su base de clientes a nivel mundial garantizando fabricación de alta calidad, rendimiento operativo, supervisión logística de alto nivel, gestión de proyectos complejos, así como innovación en valor de mercado y un reconocido compromiso con la Responsabilidad social corporativa.
Orgullosa de que la innovación sea la clave de su éxito, Albéa fabrica productos novedosos que ofrecen una mejor ergonomía, diferenciación a nivel visual, precios asequibles y un diseño moderno. La compañía también aprovecha la innovación en sus procesos, desarrollando nuevas tecnologías y procedimientos para diferenciar su packaging y hacerlo efectivo, más competitivo y más respetuoso con el medioambiente. Y lo hace estando a la altura de los desafíos técnicos de sus clientes y garantizando que se cumplan los objetivos a nivel de diseño con un precio adecuado.
La digitalización permite aumentar rápidamente la producción en varios centros de distintos países y, en algunos casos, hacer más seguros y flexibles los suministros
directora de Lanzamiento de nuevos productos de Albéa
El reto
Aumentar la flexibilidad sin sacrificar la eficiencia
“Las demandas constantemente cambiantes del consumidor, junto con la competitividad del sector, hace que nuestros clientes busquen siempre plazos de entrega más cortos y pedidos de cantidades inferiores”, ha explicado Valérie Lebelt, directora de Lanzamiento de nuevos productos de Albéa. “Con estrategias que exigen diversos lanzamientos, diferenciación visual y cumplir con los objetivos de sostenibilidad, el mercado de tubos para cosmética ya estaba pasando por un momento complicado, que no ha hecho más que empeorar durante la reciente crisis del coronavirus (COVID-19).
“Para dar respuesta a estas crecientes demandas, Albéa está revolucionando el proceso de desarrollo de nuestros principales productos, aprovechando la tecnología digital como parte de la solución para aumentar la flexibilidad”, ha comentado Valérie. “Nos dimos cuenta de que la tecnología digital era la respuesta para seguir satisfaciendo las peticiones de nuestros clientes, que precisaban agilidad, capacidad de respuesta, innovación y fiabilidad. La digitalización de nuestros procesos permitiría agilizar ciertas fases técnicas y, a la par, hacerlas más fiables. También nos permitiría gestionar proyectos de manera más colaborativa y garantizar transparencia integral durante el ciclo de vida de un proyecto.
“La digitalización permite aumentar rápidamente la producción en varios centros de distintos países y, en algunos casos, hacer más seguros y flexibles los suministros”, ha añadido Valérie. “A nivel técnico, la impresión digital conlleva muchas ventajas en lo que respecta a la velocidad de ejecución, la agilidad y la personalización, todo ello muy interesante. Pero sabemos que, en la práctica, comprar un prensa digital no es suficiente. El resultado solo puede ser fiable si se domina el proceso inicial y aquí es donde fue tan importante trabajar con Esko.”
WebCenter nos permitió no solo gestionar de manera efectiva nuestra cartera de proyectos, sino también ofrecer altos niveles de eficiencia, una priorización constante y sencilla y, por lo tanto, una capacidad de respuesta óptima a nuestros clientes
directora de Lanzamiento de nuevos productos de Albéa
La solución
Procesos de preimpresión colaborativos, eficientes y controlados
“Trabajamos estrechamente con Esko para desarrollar herramientas de preimpresión, así como una plataforma colaborativa para gestionar proyectos en nuestras instalaciones industriales, en nuestros distintos centros y también directamente con nuestros clientes y sus agencias de diseño”, ha señalado Valérie. “Esko WebCenter nos permitió no solo gestionar de manera efectiva nuestra cartera de proyectos, sino también ofrecer altos niveles de eficiencia, una priorización constante y sencilla y, por lo tanto, una capacidad de respuesta óptima a nuestros clientes.”
WebCenter es una plataforma potente para la administración y colaboración de packaging que permite a empresas de cualquier tamaño digitalizar sus procesos y afrontar los retos actuales con confianza. El software seguro basado en web ha sido elaborado para ayudar a los convertidores de packaging a atender las exigencias de un entorno empresarial en constante evolución.
Gestionando todos los aspectos de las especificaciones de preproducción, la aprobación y el ciclo de vida del proyecto para eliminar los cuellos de botella más típicos desde el diseño hasta la producción de packaging, WebCenter es la única solución del mercado desarrollada específicamente para el sector del packaging. El proceso de aprobación integrado muestra cuándo se ha enviado un activo para su aprobación, quién es el aprobador y cuándo se ha aprobado antes de que el software active automáticamente y de inmediato las siguientes tareas; y todo, en tiempo real.
“El factor tiempo de acceso al mercado es cada vez más importante en nuestro sector”, ha señalado Valérie. “Hace apenas unos años, lo normal y aceptable era que el proceso de creación un nuevo producto pudiera llevar en torno a tres meses, pero hoy en día se espera que la entrega se realice en apenas de cuatro a seis semanas. Con WebCenter, podemos reducir nuestro tiempo de acceso al mercado y controlar totalmente la calidad de ejecución del proyecto.”
Hace apenas unos años, lo normal y aceptable era que el proceso de creación un nuevo producto pudiera llevar en torno a tres meses, pero hoy en día se espera que la entrega se realice en apenas de cuatro a seis semanas. Con WebCenter, podemos reducir nuestro tiempo de acceso al mercado y controlar totalmente la calidad de ejecución del proyecto.
directora de Lanzamiento de nuevos productos de Albéa
Las ventajas
Flexibilidad con calidad garantizada gracias a la estandarización
“La flexibilidad que ofrece WebCenter en materia de priorización y capacidad de respuesta ha sido un activo vital durante la crisis mundial”, ha comentado Valérie. “Supuso que, como empresa, no tuviéramos que parar por la falta de abastecimiento de un proveedor concreto o de un país determinado. Contábamos con la flexibilidad de podernos adaptar rápidamente ante cualquier cambio repentino en el mercado; podíamos trasladar la producción de un centro a otro en función de las restricciones y oportunidades de la cadena de suministro.”
Valérie ha explicado que, al digitalizarse, Albéa ha eliminado las modificaciones necesarias al final de la línea de producción, lo que ha generado nuevas necesidades al inicio, en la etapa de la preimpresión. “Como siempre hay que ir más rápido, debemos estar seguros de dominar la etapa de la preimpresión, así como el desarrollo del color y el diseño de las herramientas”, ha comentado. “Así pues, controlar la cadena gráfica al completo es una cuestión de calidad y también de tiempo de acceso al mercado. Esko ha sido un auténtico colaborador en la transformación digital de nuestro proceso de desarrollo de packaging impreso.
“Un ejemplo es cómo se incluye la estandarización de la secuencia de colores en un archivo digital”, ha explicado. “Ese archivo nos permite ofrecer una prueba a nuestros clientes, una renderización parecida a una prueba de impresión realizada en un equipo industrial en nuestros centros, pero que en realidad se realiza offline, en pequeñas impresoras digitales calibradas para cada tipo de tubo.
“Nuestros clientes reciben siempre una muestra real y la capacidad de mantener ese proceso ha sido especialmente importante durante la pandemia”, ha señalado Valérie. “Obviamente, la diversas restricciones que todos hemos sufrido han limitado los viajes y la posibilidad de vernos en persona, por lo que poder obtener una aprobación rápida vía correo electrónico u ordinario nos ha ayudado a lograr importantes ahorros”, ha añadido. “Mientras una prueba de color tradicional, realizada in situ en una línea industrial, puede llevar entre cuatro y seis semanas y precisa 300 kilos de materiales plásticos, con WebCenter en plena etapa de generación de pruebas, ahora solo hacen falta unos días y 150 gramos de resinas. Significa dos mil veces menos material, con los importantes ahorros consecuentes, así como reducir el impacto en el medioambiente.”
Valérie ha señalado que seguirán implantando WebCenter en la empresa y que será especialmente útil en el proceso de desarrollo de nuevos productos. “Nuestra plataforma colaborativa y segura también estará abierta a nuestros clientes”, ha dicho. “Podrán interactuar directamente con nuestros expertos, no solo para previsualizar la renderización de sus diseños, sino también para validar todo el desarrollo del tubo, incluido el color del cuerpo y del tapón.
“Esto supondrá que desarrollar un tubo nuevo sea un proceso colaborativo, eficiente y rápido, lo que también ahorra tiempo, dinero y plástico, y reduce las emisiones de dióxido de carbono.”
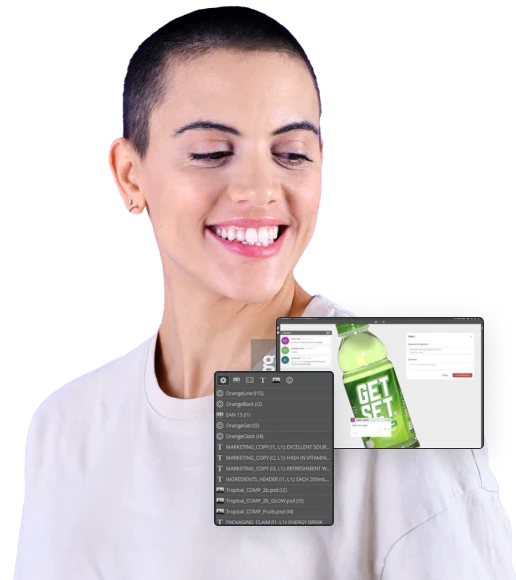