Reynders logra importantes beneficios a nivel de eficiencia operativa gracias a CDI Crystal, XPS Crystal y PlateHandler Automático
La cambiante dinámica del mercado y las impredecibles fluctuaciones de la demanda hacían necesaria una simplificación del proceso de confección de planchas para aumentar la eficiencia en Reynders.
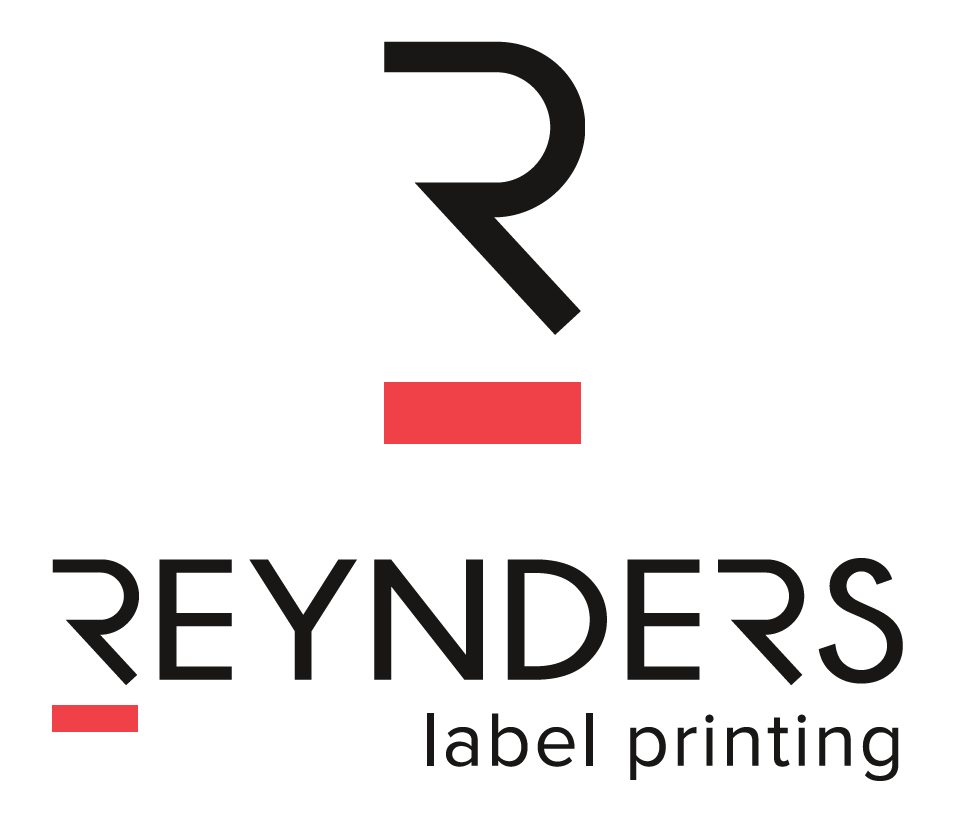
El cliente
Ocho mil millones de etiquetas anuales
Fundada hace más de 60 años y con sede en Boechout, Bélgica, Reynders es una de las principales empresas internacionales de impresión de etiquetas. Con más de 500 empleados repartidos en siete centros de cinco países de Europa y Asia, Reynders imprime más de ocho mil millones de etiquetas al año.
Con décadas de experiencia en la impresión de etiquetas, actualmente el negocio de Reynders opera con éxito en los mercados: alimentación y bebida, farmacéutico, cosmética, industrial, automoción, química y productos para el hogar. Dedicada a la producción de etiquetas autoadhesivas, camisas, packaging flexible y etiquetas en molde, ha diversificado su negocio a lo largo de los años y ha desarrollado una cultura centrada en la hiper-eficiencia, pero mejorada con un toque personal para los clientes. Las claves del éxito de la empresa son: consistencia, estandarización y centralización.
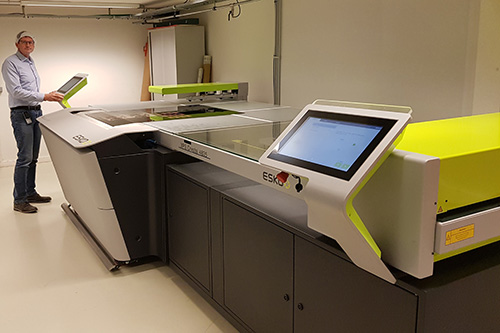
El reto
Un proceso de confección de planchas manual dificulta la flexibilidad y la eficiencia operativa en la preimpresión
Aunque Automation Engine de Esko funciona como un servidor de flujos de trabajo central para la operativa de Reynders, permitiendo que los archivos de preimpresión digitales fluyan fácilmente entre los centros de la empresa, el proceso de confección de planchas de preimpresión del centro de Boechout se había quedado obsoleto, explica André Vandepitte, director de Preimpresión.
“El 2020 ha sido un año muy raro, con impredecibles fluctuaciones de la demanda a causa de la pandemia de la Covid-19. No obstante, en Reynders hemos tenido mucha suerte. Dado que somos un proveedor esencial de los crecientes mercados farmacéutico y de alimentación y bebida, hemos experimentado un aumento de la demanda de productos de etiquetas y hemos tenido mucho trabajo. Por suerte, hace alrededor de un año, invertimos en una gama de hardware de Esko que galvanizó nuestra capacidad de satisfacer esa enorme y creciente demanda en nuestro departamento de preimpresión.”
“Aquí, en Boechout, suministramos planchas de flexografía a nuestras empresas francesas y belgas y trabajábamos con un CDI antiguo de Esko con dos unidades de exposición. Pero nuestras planchas son muy pequeñas (dado que nos dedicamos a la impresión de etiquetas) y eran necesarios varios pasos manuales para finalizar un solo trabajo, lo que causaba importantes ineficiencias de personal.”
“Para finalizar el proceso de exposición, teníamos que mover una plancha cuatro veces entre las varias partes del sistema y, al final, transferirlas al proceso de lavado. Era laborioso y ocupaba mucho tiempo de nuestros operarios para simplemente ir moviendo las planchas. Además, nuestras exposiciones no eran consistentes. Con el antiguo sistema de lámparas, teníamos que estar constantemente comprobando, midiendo y controlando el rendimiento para lograr la calidad de plancha deseada. Básicamente, perdíamos mucho tiempo en trabajo que no añadía valor y no lográbamos la capacidad deseada.”
Hemos pasado de mover planchas de una máquina a otra a un proceso automatizado, integrado y optimizado que funciona pulsando un mero botón.
director de Preimpresión de Reynders, Bélgica
La solución
Reynders invierte en CDI, XPS y PlateHandler Automático de Esko para aumentar la velocidad de producción de planchas y potenciar aún más la calidad
En 2019, Reynders invirtió en un nuevo sistema de Esko formado por CDI Crystal, XPS Crystal y PlateHandler Automático para reducir increíblemente la complejidad en la sala de planchas de Boechout. El nuevo equipo de exposición está diseñado para conectarse directamente con el dispositivo de exposición digital UV XPS Crystal. Combinando la exposición en alta resolución del láser de fibra con la exposición patentada delantera y trasera por UV LED del XPS Crystal, se producen planchas digitales de flexografía con una capacidad de reproducción y calidad únicas.
Además, Reynders tomó la decisión de invertir en el PlateHandler Automático de Esko. El nuevo PlateHandler Automático proporcionó la oportunidad de crear un proceso de producción de planchas sin contacto hasta el lavado, lo que garantiza importantes beneficios en tiempo de operario, y eficiencia en la confección de planchas.
El PlateHandler, un robot que conecta el CDI Crystal con el XPS Crystal, reduce la cantidad de intervenciones manuales del operario y los gastos de funcionamiento. Integrar el equipo de confección de planchas para flexografía libera hasta el 50 % del tiempo de operario para que este pueda realizar otras tareas más valiosas, como el control de calidad, el almacenamiento de planchas o el montaje de planchas.
Nuestros operarios quedan libres para centrarse en trabajos de valor añadido y ahora podemos funcionar con una sola persona por turno, lo que es mucho más rentable y eficiente.
director de Preimpresión de Reynders, Bélgica
Las ventajas
La calidad y la consistencia de las planchas aumentan aún más y los operarios tienen más tiempo para trabajar en tareas de valor añadido
“Invertir en un conjunto integrado de hardware para la confección de planchas ha simplificado totalmente nuestro proceso. Hemos pasado de tener personal corriendo de un lado a otro moviendo planchas de una máquina a otra, a un proceso automatizado, integrado y optimizado que funciona pulsando un mero botón”, ha comentado André.
“Añadir el PlateHandler Automático a la ecuación ha aportado que nuestros operarios dispongan de mucho más tiempo productivo. Quedan libres para centrarse en trabajos de mayor valor añadido y ahora podemos funcionar con una sola persona por turno (en nuestro sistema de dos turnos), lo que es mucho más rentable y eficiente.”
“Además, también estamos detectando mucha más estabilidad en nuestras planchas. En vez de tener que comprobar constantemente si las lámparas se calientan correctamente o estar solucionando problemas, ahora obtenemos resultados consistentes del XPS Crystal y no tenemos que preocuparnos. Esto también libera tiempo de nuestros operarios, que ya no tienen que estar constantemente comprobando y midiendo el resultado de las lámparas, ya que los LED están simplemente encendidos o apagados.”
“Por supuesto, al tener que alimentar más de 50 prensas de flexografía y digitales en todo el Grupo, la preimpresión se puede convertir en un verdadero cuello de botella si no se gestiona eficientemente. Nuestra relación con Esko se remonta a muchos años atrás y era la elección obvia a la hora de invertir en nuestra capacidad de preimpresión. Dado nuestro nivel de integración actual, contamos con calidad, consistencia y capacidad de confección de planchas no solo para satisfacer las necesidades de nuestros clientes, sino también para superarlas día tras día.”
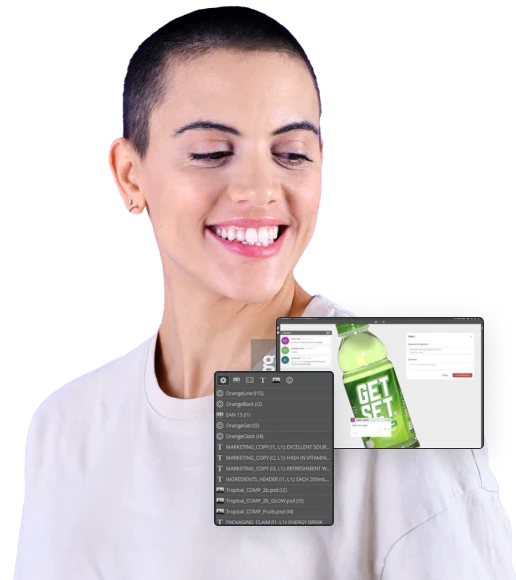