Great Northern Maximizes Pallet Arrangement and Delivers Accurate Reports Faster with Cloud-Based Cape Pack
Great Northern benefits from more effective palletization and improves fulfillment efficiency with Esko software.

The modular software helps determine the best product size, case count, product arrangement, case size, pallet and container load, enabling businesses like Great Northern to optimize their packaging for shipping. The software can create new case sizes, build efficient pallet patterns, analyze compression strength of cases and pallets, and improve material and cube utilization.
Integrated for Speed and Efficiency
“We have five locations using Cape across the different Great Northern sites, ranging between two and ten users at each site, so that’s around forty different users on a daily basis,” said Brett Vavra, Structural Designer with Great Northern, based at the Chippewa Falls facility.
“WebCenter, ArtiosCAD Enterprise and Cape Pack have already helped our design departments run more efficiently in a fast-paced environment,” he said. “One of the top things with Cape Pack going to the cloud is that now everything is just on one page and one platform so it’s so much easier and faster for all our users to work with Cape, calculate solutions, create a report and save it directly into WebCenter. All our designs from ArtiosCAD are also centralized in WebCenter and from Cape we can now easily save our pallet reports into WebCenter too.
It’s a great solution for us from a commercial design perspective, as we’re trying to maximize a pallet’s efficiency. From the get-go I can use Cape to help determine what size of box and inserts I should use. With the cloudbased Cape Pack, it’s so much more userfriendly, intuitive and easy to use. Compared to the early days and the desktop version, Cape Pack just gets better and better.
Structural Designer, Great Northern
Fulfilling Needs
Mike Dorazio, Senior Structural Designer with Great Northern, also based at Chippewa Falls, said the software had been incredibly helpful in the fulfillment department, where employee turnover is high and therefore the workforce is not as experienced.
“A huge pain point for us was the high turnover in that area – and Cape Pack has really helped improve fulfillment efficiency,” he said. “We’re now able to put all details of the cornerboard, stretch wrap, banding and even layer pads on there and create a realistic picture of the unit,” he explained. “This really helps our new employees that need that visual representation of what a unit should look like, which helps get jobs done in a timely manner.”
Brett was quick to agree. “Customizing the layers is very user friendly. You can move things around, using a middle support if necessary, and I can move displays around to fit them on the pallet in the best way,” he said.
“The new Format Load function has been great too. I’m more on the display side, and for that we use a lot of mini pallets. With many of our construction retailers, like Home Depot, we’re dealing with a lot of quarter-pallet displays, which need that mini pallet, and the new fill master pallet function really shows the picture of the mini-pallet on the master pallet, which helps our fulfillment department create unitizations.
Format Load has been a game changer for us. It helps our fulfillment team build palletized units better, quicker and easier.
Senior Structural Designer, Great Northern
Better Reports, Faster
“The new improved reporting functionality is great too,” said Mike. “We can go step by step to produce, access and edit reports to meet specific customer demands, tailoring the reports very quickly and including all the data they require.”
With Cape Pack being cloud-based, the reports can be accessed by all personnel regardless of location, working any shift time. Users can create a PDF for local download or email a link to the recipient to view the report in the cloud.
Mike added: “You can now make the report more relatable to your own brand too, with images, logos, colors of the package to reflect corporate colors etc, so when a customer receives our report they know they got it from Great Northern. It’s been great being able to customize those.”
There’s been a real increase in efficiency. Everything’s on one page, we can enter the data and spit out a solution in just a minute. It’s very fast and keeps getting faster.
Structural Designer, Great Northern
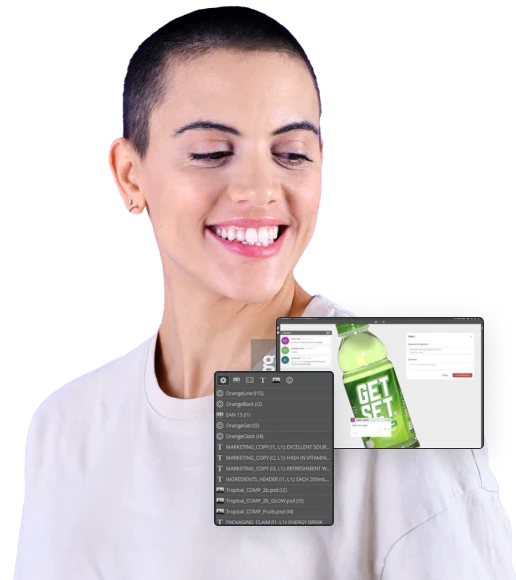