
“Our two XPS Crystal 4260 systems have taken a few worry lines off our faces. The process is characterised by unprecedented stability and uniformity,” says Torben Segelken, Managing Director of Carl Ostermann Erben GmbH (coe) in Stuhr-Moordeich near Bremen. “Of course, we also had our previous tube imagesetters under control. But we had to put in a lot of effort to continuously achieve the desired quality. Among other things, we had to check and record the condition of the tubes on a weekly basis and adjust the exposure times.”
These times are over since the commissioning of the two XPS Crystal 4260 systems from Esko in November 2023 and at the end of March 2024. A special feature of this Esko technology, which has won many prizes including the Intertech Technology Award, is that it carries out UV LED exposure of the main and reverse sides simultaneously. This synchronisation of the main and back exposure is one of the several reasons why the XPS Crystal systems always produce a repeatable and consistent plate quality. In addition, their LEDs continuously emit a uniform light. In contrast, tube platesetters emit UV radiation that varies in intensity depending on the individual tube and the position within the tubes and is also not constant. This causes fluctuations in the exposure process and therefore also in the plates. With XPS Crystal systems, these are excluded. The ‘floor’ of the flexographic printing plates produced with them is absolutely flat. The reliefs are completely flat.
Certified Process
The automation of the new technology also makes a decisive contribution to the stability and simplicity of the process. At the customer experience center in Itzehoe, Esko certifies all flexographic printing plates that are newly launched onto the market by the various manufacturers. Esko optimises the UV LED exposure process with the XPS Crystal systems in close cooperation with the printing plate manufacturers using more than 30 parameters in several printing tests at the DFTA-TZ in Stuttgart. This process results in LED recipes stored in the controls of the XPS Crystal platesetters. This has a decisive advantage for customers: their operating personnel only need to select the printing plate types to be processed in the system menu. The printing plates are then reliably produced according to the selected recipes.
In combination with the high quality and stability of the UV LED exposure, this forms the basis for the unique repeatability in the production of flexographic printing plates with the XPS Crystal systems. With these systems, Esko has set a new standard in the market. In the past four years alone, around 500 XPS Crystal systems have been installed worldwide. There are currently also around 5,000 CDI systems in operation for imaging digital flexographic printing plates. In short: with expertise in imaging and UV LED exposure, Esko is the undisputed market leader.
Carl Ostermann can process flexographic printing plates in formats up to 1,067 mm x 1,524 mm with its two XPS Crystal 4260 systems. “Our production process has become considerably leaner. Our operators only have to place the imaged printing plates on the XPS Crystal platesetters and select the printing plate type on the display. The systems then process them reliably in the desired quality,” says Segelken. Neither backside exposure tests nor washout wedges and other quality control steps are required.
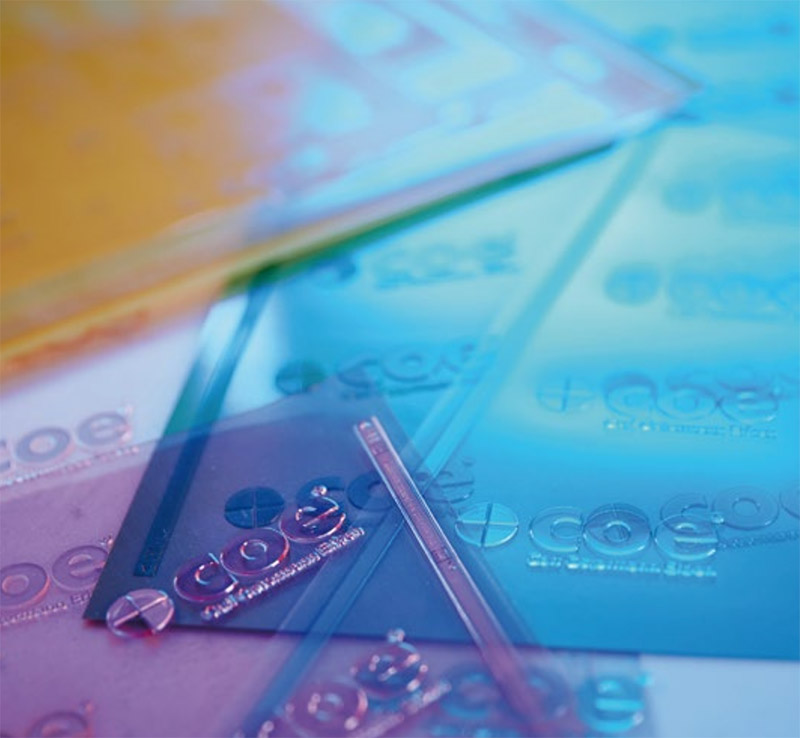
Customisable
Despite this process standardisation, Carl Ostermann’s systems offer flexible options for adjusting the parameter settings of the UV LED exposure if required and for creating different relief heights on the printing plates. This allows the company to utilise its extensive practical experience and offer customers real added value, thus setting itself apart from the competition.
Customised adaptations are necessary, for example, when customers have to work with older printing presses with a higher supply pressure and therefore require deeper reliefs. Flexibility is also particularly important for pharmaceutical customers: in this sector, the relief depths are always precisely specified and checked in the incoming goods department.
“Various parameters influence the relief depths in tube imagesetters. That’s why we normally had to play around with them and expose several test plates until we found the best values. With the XPS Crystal 4260 systems, we can determine the relief depths with tenths of a millimetre precision using a slider on the touch panel of the systems and thus easily fulfil requests for deeper reliefs,” says Segelken, praising the convenience of the process.
Smooth Changeover
Switching production to UV LED exposure was easier for the company than expected. “The intuitive operability of the process played an important role in this. It was very well received by our employees right from the start,” says Segelken, looking back.
Carl Ostermann had some concerns about customer acceptance of the new technology. Wrongly so, as it soon turned out. Segelken: “From the point of view of many of our customers, the time had also come to switch from tube platesetters to LED exposure in the production of their printing plates. For environmental reasons alone. But many customers were also aware of the qualitative advantages of the new technology.”
No More Limitations in Flexographic Printing
The flat top dot plates produced with the XPS Crystal 4260 systems now enable kiss printing in flexographic printing – and therefore a quality in this printing process that was previously reserved for gravure printing. Thanks to the absolutely flat reliefs of the printing plates, modern flexographic printing presses can work with considerably less set-off pressure, reduced ink transfer and more fluid printing inks. The printed images are free from tears, donuts, ink splashes or other artefacts. Texts are razor-sharp and even the finest lines come out without any squeezed edges. The gradients are harmonious, smooth and soft like never before. The images in turn give the impression of coming to life at any moment thanks to the brilliance and radiance of the colours.
At the same time, the service life of the printing plates is considerably extended. And when reprinting, the same quality is achieved reliably and without losses. The savings in ink consumption are around 20% with solvent-based inks. This is not just an economic advantage. It also benefits the sustainability of the packaging products and their manufacturing process. Carl Ostermann’s customers also include manufacturers of label printing machines. With its two XPS Crystal 4260 systems, the company has become even more attractive to them as a supplier.
Flexographic printing continues to grow in the market. Innovative technology from Esko for flexographic printing plate production is contributing to this. “A new customer of ours recently replaced one of its gravure presses with a flexo press,” confirms Segelken. “The plates also look great.”
Reduced Variety of Materials
In order to meet the various requirements of its customers, Carl Ostermann used to process significantly more than ten different types of panels in the past. This has also changed since the switch to LED exposure with the XPS Crystal 4260 systems. As the printing plate manufacturer had to run new fingerprints anyway, some old plate types could be retired.
“Ultimately, we will probably be able to cover the requirements of the market with a handful of plate types. “We can utilise our plates better, produce less waste and have also further increased the efficiency of our process,” says Segelken, listing other important changes. “We are not a laboratory, but more than ever we need easy-to-handle and reproducible processes, such as those offered by the XPS Crystal 4260 systems.”
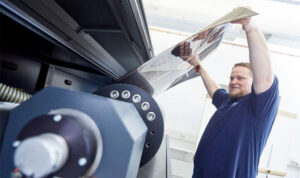
Decades of Partnership with Esko
The co-operation with Esko goes back decades. On the occasion of its 100th anniversary in September 1991, Carl Ostermann invested in digital technology from Barco-Graphics, which later became Esko. Since then, Carl Ostermann has successively implemented various software solutions from Esko, which today form the backbone of the printing plate manufacturer’s production process. Segelken: “Automation Engine in particular is a very versatile product. It has opened up a wide range of possibilities for the automation of our work processes.” As an example, he cites Carl Ostermann’s Speedy Workflow for customers who carry out their repro work themselves and only require a service provider for the production of their flexographic printing plates. These jobs no longer have to go through the entire work preparation process. They are created automatically with the help of the Automation Engine and controlled by production. The result is streamlined processes and short delivery times.
In connection with the XPS Crystal 4260 systems, the intelligent print parameter assistant Print
Control Wizzard is one of the highlights for Carl Ostermann. It is part of Esko Imaging Engine and supports the company with its intuitive user interface in the production of premium flexographic printing plates. “If we have any questions about the settings for special customer requirements, Esko Service is on hand to provide us with quick answers,” says Segelken, addressing another important aspect of the partnership with his supplier. The Flexo Excellence training was also extremely helpful during the installation of the new systems. The system operators took away valuable suggestions and tricks from it, which will benefit their day-to-day work.
Esko technology gives us all the degrees of freedom and possibilities to fulfil even special requirements. Over the decades, we have updated it time and time again and thus tightened all the efficiency screws that ensure our competitiveness in the market.
“For our customers, we are a high-end service provider that has all the necessary processes in place. This enables us to offer our customers a broad spectrum. At the same time, we are still small enough to provide them with customised support,” says Segelken, differentiating Carl Ostermann from the competition. “Esko technology gives us all the degrees of freedom and options we need to fulfil even special requirements. Over the decades, we have updated it time and time again and thus tightened all the efficiency screws that ensure our competitiveness in the market. Most recently with the XPS Crystal 4260 systems.”
About Carl Ostermann
The origins of today’s Carl Ostermann Erben GmbH (coe) with around 50 employees date back to 1891. At that time, Carl Ostermann founded a one-man business based on an idea to optimise lead casting. Today, the company has a second site in Filderstadt in addition to its headquarters in Stuhr-Moordeich near Bremen. In addition to flexographic printing plates, it produces printing plates for solvent-based, water-based and thermal printing processes, printing plates for waterless offset printing and printing screens. Carl Ostermann supplies manufacturers of labels and flexible packaging for food and drugstore products as well as pharmaceutical companies in Germany and neighbouring countries. The company is now in its fifth generation and is managed by the two managing partners Holger Ostermann and Torben Segelken.