Esko Print Control Wizard Creates Triple Benefits for Contact Originators and Customers
Contact Originators enhances prepress and print performance with Esko Print Control Wizard
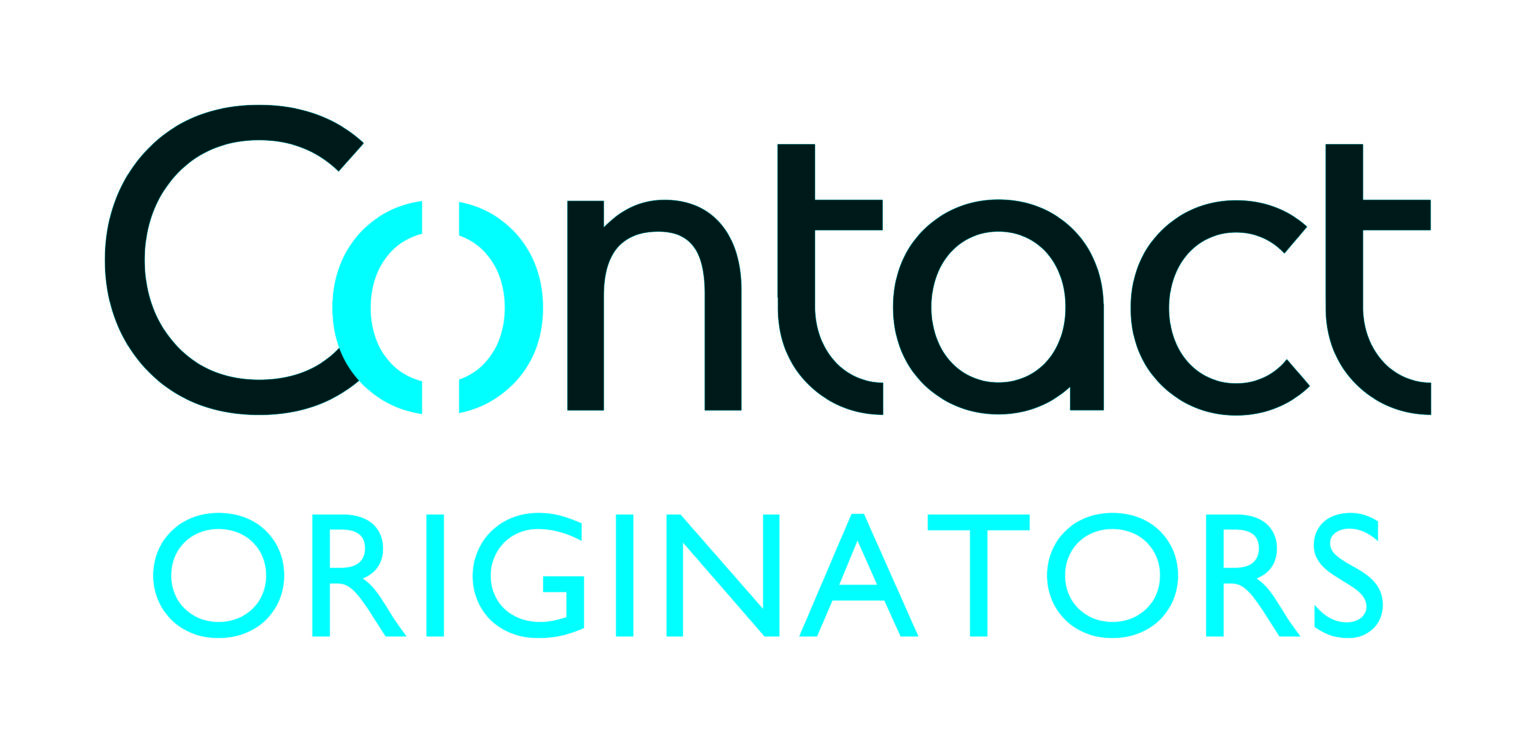
Case Study Summary
Contact Originators Group, (‘Contact’) a privately-owned company established in 1992 in Bredbury, Stockport, UK, is renowned for its innovative approach to packaging origination, graphics management and flexographic plate production. With over 70 employees, the company operates across the UK and Europe and is rightly proud of its achievement in being the first flexo platemaking company in the UK to have gained Esko HD Flexo accreditation in the corrugated industry.
The Contact Originators team’s ethos lies in ‘driving the print and brand experience through print innovation’. This absolute focus on delivering advances both in its own prepress production efficiency and quality, as well as its customers’ print performance, has assured the company of its leading market position in the UK corrugated market, as well as ensuring Contact is a beta testing partner for Esko.
Our job is to ensure our customers’ presses run as smoothly as possible with maximum graphics performance. This is where Print Control Wizard steps in.
General Manager, Contact Originators Group, UK
The Challenge
Driving innovation in a challenging print sector
Contact Originators has invested in an ecosystem of Esko technologies over the years; from WebCenter to Automation Engine, CDI Crystal to XPS Crystal. The company has a long-held view that integrated Esko hardware and software enables the most flexible, accurate and efficient prepress operation possible.
Nick Mitchell, General Manager at Contact Originators, comments: “We are the largest supplier of prepress services to the UK corrugated sector today. It’s a highly competitive industry and has been booming in recent years with the growth in e-commerce and the anti-plastics movement in packaging. Being wide format, it’s a technically challenging print sector and when combined with the lower grammage and recycled materials coming onto the market to drive down costs, we need to be constantly seeking new ways to boost our customers’ print consistency and performance. Our job is to ensure our customers’ presses run as smoothly as possible with maximum graphics performance. This is where Print Control Wizard steps in.”
Les Jones, Print Innovation Manager at Contact Originators, said: “Our corrugated customers need continuous improvement in their print processes, along with efficiency savings and superb print performance. We needed a solution that both enabled our prepress operation to handle jobs faster with ultimate accuracy, as well as deliver these improvements in print quality for them. What we were seeking was a technology that could enable our customers to meet the print standards of pre-print lithographic or digital printing with their flexographic presses, enabling them to convert business away with no compromises.”
What we’ve seen with Print Control Wizard is that plates are now more consistent, and we can produce them more quickly; which is great for a busy prepress environment like ours.
General Manager, Contact Originators Group, UK
The Solution
Print Control Wizard delivers benefits to prepress, printer and brand!
The award-winning Print Control Wizard software, part of Esko Imaging Engine, was developed to add a new level of simplification to the plate-making process. The tool uses all critical print parameters and variables – imaging resolution, exposure settings, plate, substrate, anilox, press type and inks – to standardize the generation of Crystal screens, curves and application of surface screens at low resolution within the corrugated platemaking process. At the same time, it removes all non-value-added tasks from the prepress process.
Operators utilize an intuitive wizard-style user interface that unlocks powerful functionality to quickly and easily create premium flexo plates, where partial dots are removed with Dot Clean Up functionality and tints and vignettes print clean. There is also therefore a reduced need to consider object-based screening, which means less work in prepress, a reduced risk of errors and higher efficiency not only in the converter’s press shop, but also in the prepress operations. A win for both Contact Originators and its converter customers!
“Here at Contact, what we’ve seen with Print Control Wizard is that plates are now more consistent, and we can produce them more quickly; which is great for a busy prepress environment like ours,” said Les. “However, it’s the benefits to our printer customers – and their customers, the brands – that really stand out.”
Interestingly, we’ve even had feedback from brands that they are perceiving an improvement in graphics quality and impact, even on low grammage uncoated liners for shelf ready packaging.
General Manager, Contact Originators Group, UK
The Benefits
Boosting overall equipment efficiency
“First, we are seeing more color density for less ink laydown on low grammage and/or recycled test liners. Printers are also reporting that they are definitely achieving improved final print results in less time, with associated improvements in material and ink waste – a real bonus in today’s cost and sustainability focused industry!” said Les.
“We estimate that Print Control Wizard is enabling our customers to save up to 20% on ink formulation too. Working in partnership with them, we are seeing more precision on each job enabling less rework or waste, and using Print Control Wizard they can print solids, tone and test work from a single plate. In real terms, this means they’re making savings on the number of plates used, as well as reducing set up times and ink consumption. We know that the benefits to the printer will vary from user to user, but the advantages of being able to print solids, tone and test are clear,” he added.
Esko has designed Print Control Wizard to reduce press stops for plate cleaning and make-ready times, boosting overall equipment efficiency. It also enables printers to move to fixed palette printing due to the consistency Print Control Wizard brings on press.
Nick continued: “Interestingly, we’ve even had feedback from brands that they are perceiving an improvement in graphics quality and impact, even on low-grammage uncoated liners for shelf-ready packaging. We know that our customers can now print flexo with a full clean vignette, with reduced dot bridging and more robust highlights, which reduces or removes the ‘hard edge’ often seen in this type of print technique. Along with the removal of any grainy images, Print Control Wizard is truly taking a step forward for the corrugated printing sector. We are delighted to be a pre-release partner for Esko, showcasing the innovation that both our companies can bring to the market.”
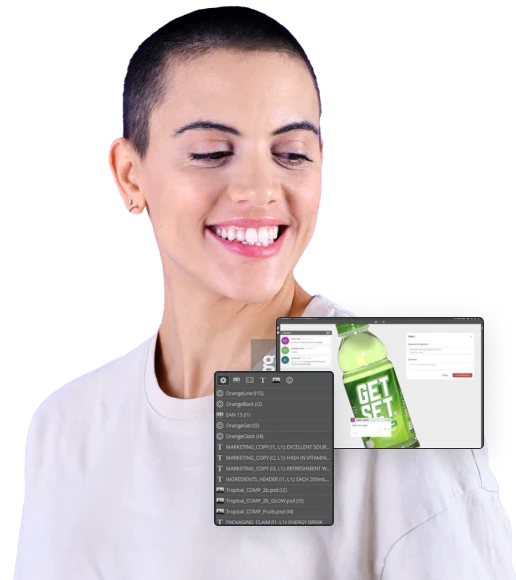